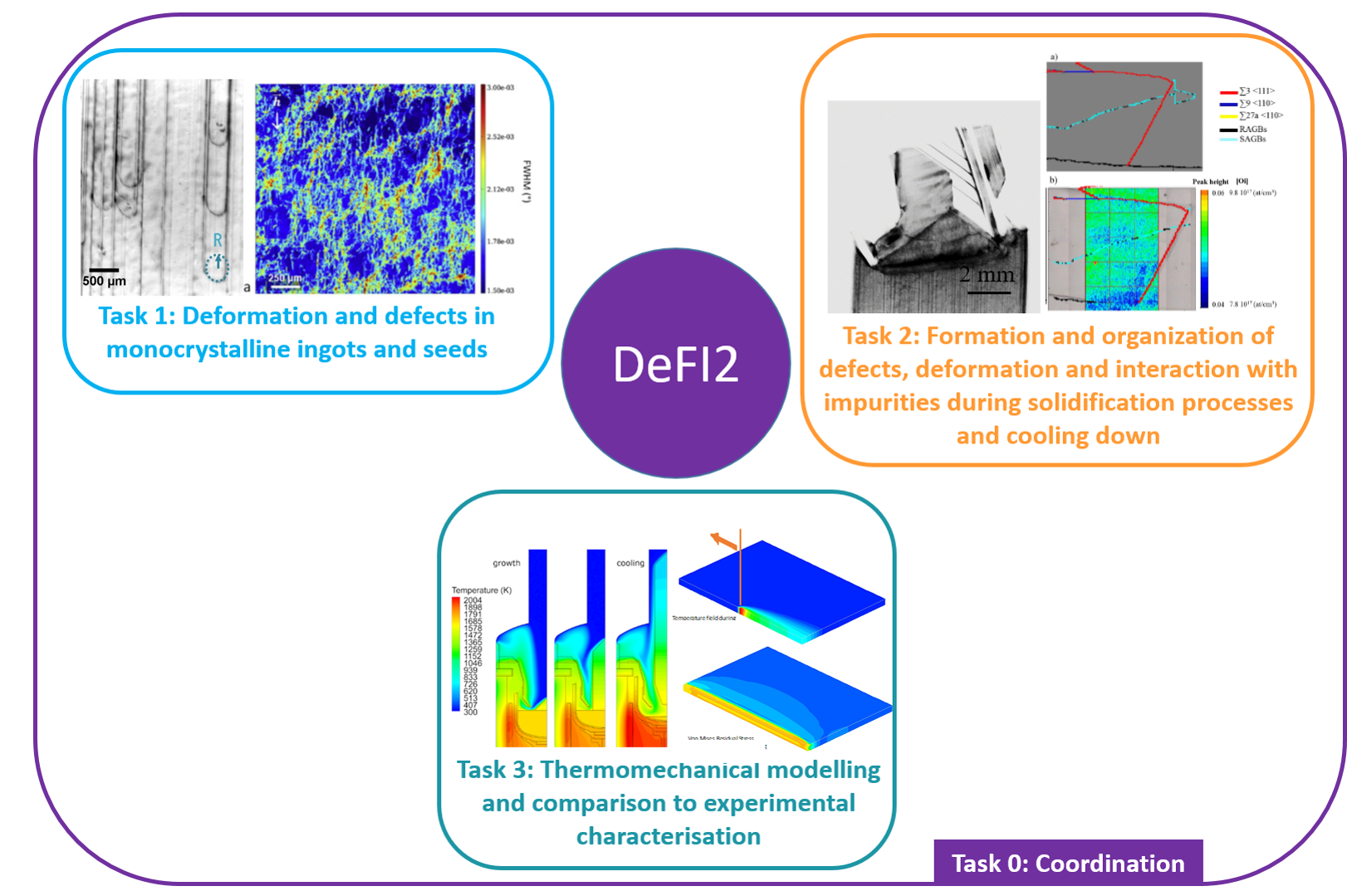
Defects and deformation in crystalline silicon ingots for photovoltaic applications towards the industrial processes
Task 0 : Coordination.
Partner : IM2NP (Leader: Nathalie Mangelinck-Noël)
Task 1: Deformation and defects in monocrystalline ingots and seeds
Partner in charge: DTS – Département des Technologies Solaires (Leader: Etienne Pihan).
The objectives of task 1 are first to select and characterise the relevant Si samples and seeds to be studied during the project. Then, knowledge on dislocation structures and associated deformations inside the seeds during heating, during the initial stages of growth or after cooling down of the seed to clearly distinguish these defects from the grown-in defects (solid-liquid interface and epitaxy) will be generated. The unique and original GaTSBI (Growth at high Temperature observed by Synchrotron Beam Imaging furnace) device developed by IM2NP will be implemented to characterize in situ the dynamics of deformation and structural defects during heating, solidification and cooling down [10, 30]. Rocking Curve Imaging (RCI) is another original method that will be used by both DTS and IM2NP to characterise quantitatively the distorted regions and defects in the studied samples. This task has been divided in four sub-tasks.
Sub-task 1.1: Selection and characterisation of samples and seeds from relevant processes and with known impurity and dopant contents.
Sub-task 1.2: Formation of defects (dislocations and sub-grains) and deformation during heating.
Sub-task 1.3: Effect of cooling down.
Sub-task 1.4: First stages of growth from monocrystalline seeds.
Task 2: Formation and organization of defects, deformation and interaction with impurities during solidification processes and cooling down
Partner in charge: IM2NP – Institut Matériaux Microélectronique Nanosciences de Provence (leader: Nathalie Mangelinck-Noël).
The first objective of task 2 is to generate knowledge on the initiation and propagation of dislocations, sub-grains and deformation during solidification. Moreover, the impact of these defects on grain nucleation and their interaction will be studied. Within this task, we will also correlate defects in general to the properties of the material. For all sub-tasks, complementary tools are selected to obtain a full characterisation of the mechanisms and defects. Model samples or samples directly issued from as-grown ingots selected in task 1 will be studied which will ensure that the results can be up-scaled to industrial ingot problematics. In situ X-ray imaging and RCI will be implemented in task 2 as in task 1. Moreover, HR-EBSD will be used by MSMP to quantify strain/stress by the cross-correlation method. Two characterisation techniques of the impurities will be used: FTIR (Fourier Transform Infra-Red) for interstitial O including local investigations at the level of structural defects (µFTIR) and light scattering tomography at IM2NP and DTS, respectively. Electrical characterization with local and global measurements (Quasi Steady State Photo Conductance/QSSPC, microwave phase shift/µW-PS) will be achieved by IM2NP and DTS. Task 2 has been divided in five sub-tasks.
Sub-task 2.1: Propagation of dislocations and deformation building during solidification.
Sub-task 2.2: Sub-grain formation and propagation.
Sub-task 2.3: Effect of the deformation on grain nucleation and dislocation emission.
Sub-task 2.4: Interaction between defects and with impurities.
Sub-task 2.5: Correlation between identified defects and the electrical properties.
Task 3: Thermomechanical modelling and comparison to experimental characterisation:
Partner in charge: MSMP – Laboratoire Mécanique, Surface, Matériaux et Procédés (Leader: Laurent Barrallier).
The objectives of task 3 are to develop validated thermomechanical models at the scale of the ingot and furnace and at the scale of the grains and defect-related stress concentrators. Thermomechanical modelling at the ingot scale will be achieved by MSMP using finite-elements (FE) with the input from the thermal simulation at the ingot scale from DTS. The model will be validated within DeFI2 with dedicated experiments. MSMP will also develop simulations of induced deformation, elastic anisotropy at grain level and stress concentrators (precipitates, grain boundaries…). This task have been divided in three sub-tasks.
Sub-task 3.1: 3D thermomechanical modelling at the scale of the furnaces.
Sub-task 3.2: Model validation by measuring temperature fields and residual stress/strain fields.
Sub-task 3.3: Thermomechanical modelling down to the grain scale including defect-related stress concentrators.